
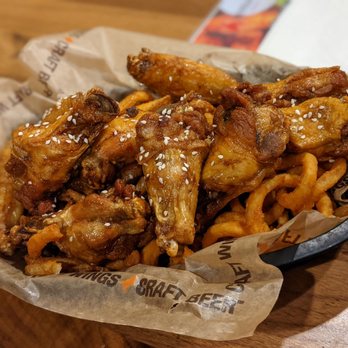
“Marshall is an approved manufacturer but parts come from all over the world. “It’s an eight-month visit for a C130 to Marshall’s, taking it down to its structure, examining it for defects, taking X-rays all over the aircraft to look for corrosion which can’t be seen by eye, spotting anything which hasn’t been picked up.” A hangar at Marshall Aerospace and Defence in Cambridge shows the scale of the operation off Newmarket RoadĪnd Marshall makes some of the parts for the C130 repairs? When the aircraft comes in we strip it down to the bare minimum and rebuild it from there. We do heavy maintenance on C130s – everything that can be done. I was inputted straight into the business as my time at Virgin Atlantic was taken forward. “There’s eight of us in the Marshall apprentice programme. “Then Covid struck hard and one of the cuts was the apprenticeship programme, but the bosses there all had connections and managed to rehome us.
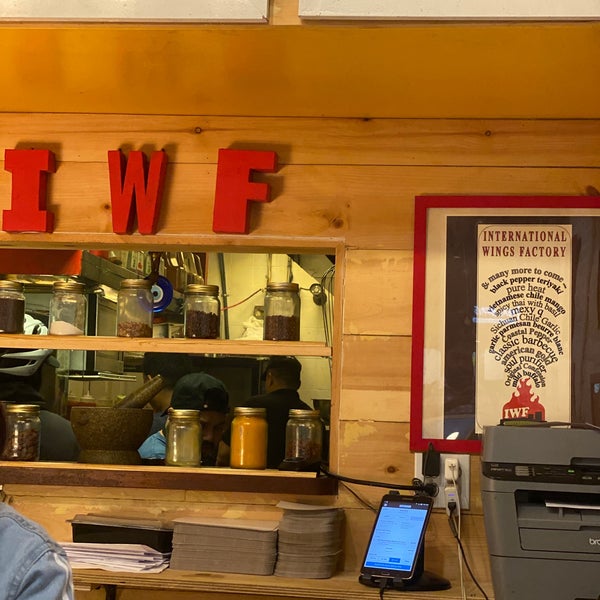
“I started the Virgin Atlantic apprenticeship programme two and a half years ago based out of Gatwick,” he says.

He began his career as an apprentice at Virgin Atlantic and moved over to Marshall Aerospace when he was made redundant due to Covid in 2020. He’s in the third year of his apprenticeship. Jeremy has been in Cambridge since January this year. “There was only one task I ran out of time on, but a lot of the tasks were designed so you can’t finish it in the time allotted, just to see how far you got.” “I completed everything pretty confidently,” notes Jeremy. The tasks included an insert repair, a primary flight control unit removal with restricted access, a daily inspection of a helicopter, control rigging on a Gazelle helicopter, a hydraulic design and set-up, and a borescope inspection. The final involved completing several timed tasks in a round-robin style set-up. “We ate together in the evenings, it was all good.” A US Marine Corps KC-130J at Cambridge Airport for routine maintenance by Marshall Aerospace and Defence Group. “We all got on really well,” adds Jeremy, who is French-American and was born in Aberdeen. “Normally with WorldSkills the final is at the NEC in Birmingham for a week, with all the other categories like hairdressing, cooking and beauty, but this year each final was held separately. “The final was held on board HMS Sultan in Gosport,” Jeremy says. The design was provided so it was just to do the manufacture, but they left out a couple of bits, like the dimensions, so there were choices to be made.”Įight finalists were selected from the 22 in the qualifying round. “The marking scheme meant they watched me build the magazine rack, took loads of pictures, and sent them off to the organisers. “It’s normally held in one place but this year you’re assigned someone from your work such as a team leader or a fully qualified engineer,” explains Jeremy. This was followed by the qualifier round, which involved building a magazine stand out of sheet metal and rivets to specifications set by the team at WorldSkills and judged by an experienced technician at Marshall Aerospace. In the UK the categories for the annual showcase include ‘engineering and technology’, ‘health and hospitality’, and ‘digital, business & creative’.Īfter the initial application, Jeremy was asked to do a basic test to ensure he was suitable to compete. Today it is active in more than 80 countries. The WorldSkills movement started in the 1950s, to celebrate and build confidence among young people through skills support. Marshall apprentice Jeremy Franks, who struck gold in the Aeronautical Engineering Mechanical category at WorldSkills 2021, described participating in the competition as “a good experience”.
